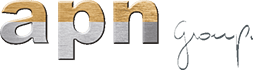
Maintenance of cutting tools
- Home
- Our services
- maintenance
Sharpening for durable tools
The efficacy of a cutting tool can be reduced due to constant friction against any sort of machined materials, which can cause rounding or breakage of its cutting angles. The tool’s cutting capacity deteriorates as a result.
That is why all of our production sites have specialised machines and a space dedicated to reconditioning worn or broken tools.
Worn tools are sharpened depending on their original features (geometry, coating) as single parts or small series. We sharpen and repair all cutting tools in carbide, HSS and PCD, such as milling cutters, drill bits, inserts and reamers.
We also maintain custom form tools.
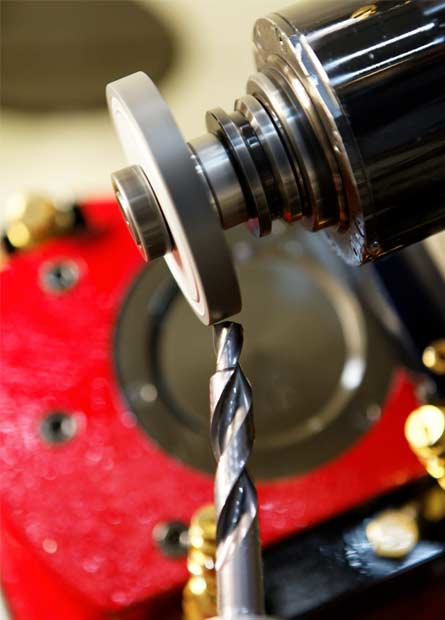
Economic and environmental benefits
Cutting tool maintenance delivers significant economic and environmental benefits. Sharpening helps extend the lifespan of tools, which results in substantial long-term savings.
Maintaining cutting tools helps retain their efficacy and precision, reducing costs linked to the purchase of new tools. Also, sharpening is cheaper than buying new products.
In terms of the environment, sharpening helps reduce waste. By keeping tools in good working order, we reduce the amount of waste.
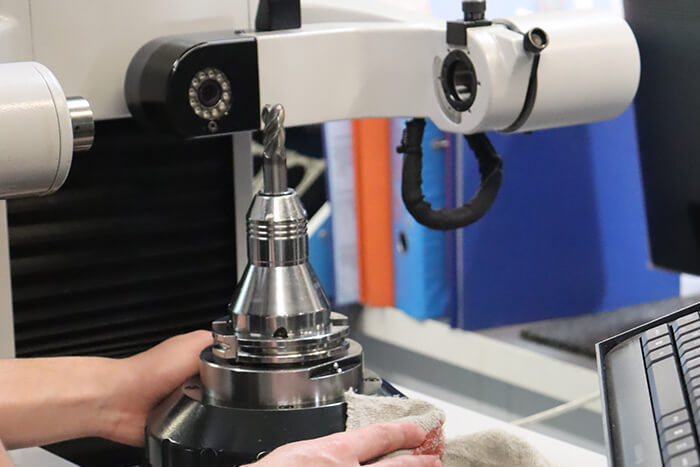
Technical coating
In order to improve tool performance and longevity, we recommend adding a coating. Thanks to our trusted partners, we can guarantee a complete service, including:
- Quality of the coating
- Speed of execution
- The post-sales service
The coating process involves getting gaseous chemical reagents to react on the heated surface of the tool, in order to form a solid layer on the surface. We can obtain coatings with specific properties tailored to the cutting requirements, such as increased heat resistance for high-temperature operations or reduced swarf adherence to help with removal during machining.
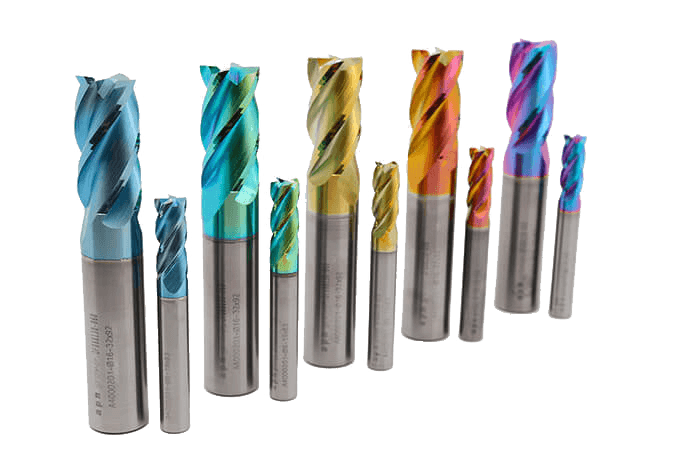