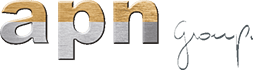
Manufacturing cutting tools
- Home
- Our services
- manufacturing
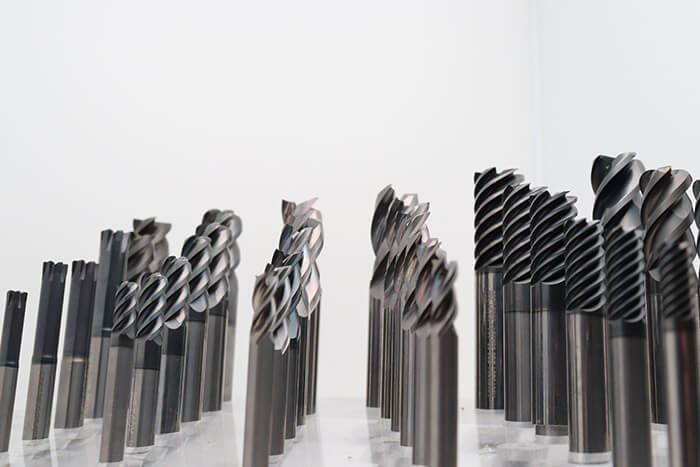
Our recognised expertise is based on know-how shared across all our production sites. We are committed to achieving excellence in the design and manufacture of cutting tools, offering effective and durable solutions.
Our workshops are equipped with state-of-the-art machines to manufacture rotating and static cutting tools. Whether for working composites, ceramics, metal, plastic or other materials, we have the expertise and resources required to design the most efficient tools.
Cutting tools play an essential role in many industrial fields. They help carry out highly precise and effective machining operations. Whether for aerospace, aviation, automotive, medical, food, general mechanical or the nuclear industry, cutting tools are essential.
We follow strict manufacturing protocols to guarantee the quality and durability of our parts. From the initial design through to modelling, plus the choice of appropriate materials, we ensure that each tool meets our customers’ specific requirements.
The key stages of the manufacturing process
- Tool cutting based on a drawing defined by the research department
- Checking dimensions based on the required tolerances.
- Laser engraving of the tool for identification purposes (reference + manufacturing order)
- Application of coating or not (heat treatment)
- Storage or dispatch
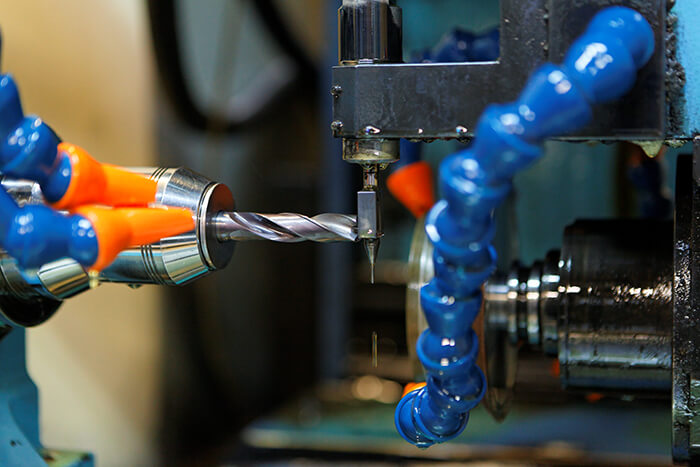
Mass and custom tool manufacturing
We are perfectly equipped to meet demand for standard and specific tools. Thanks to our tailored production methods, we are able to manufacture a huge range of cutting tools such as milling cutters, form milling cutters, drill bits, insert tool holders, inserts, quick-change ends, reamers and in different materials such as solid carbide, high-speed steel (HSS), PCD and CBN.
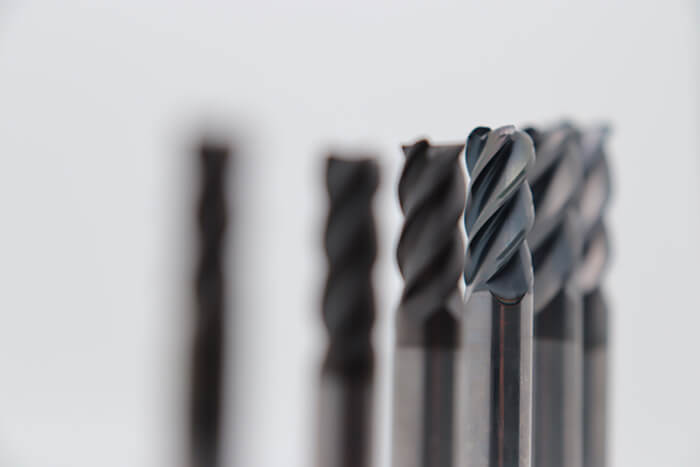
Quality control
As part of our manufacturing process, we pay close attention to quality control at every stage. We follow strict standards to guarantee the compliance and reliability of our products.
Throughout this process, we carry out regular checks to ensure quality at each stage of tool manufacturing. Precise dimension measurements are taken using state-of-the-art metrology equipment to check that parts comply with the required specifications.
The documentation drafted from the start of the design through to the final manufacturing stage is validated throughout the process. It is then archived to ensure traceability and reliable repeatability.
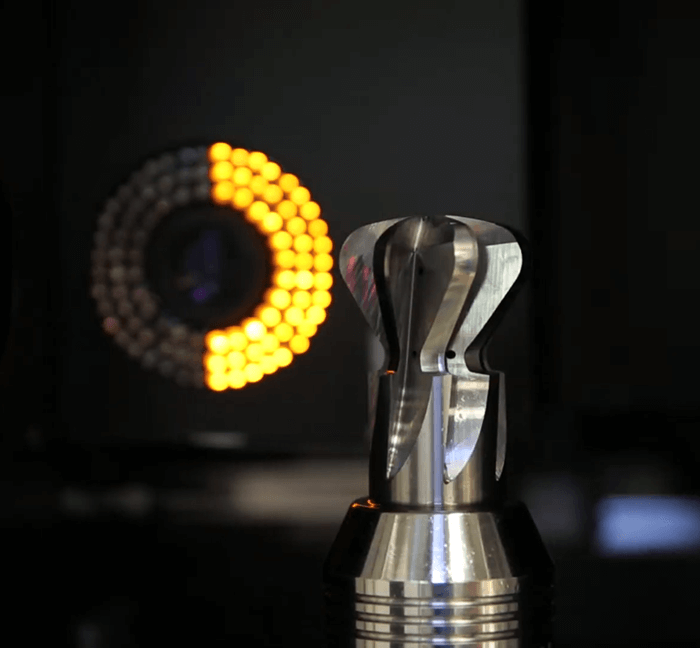